Our safety resources include a range of free, downloadable publications, advisories, checklists and other useful documents.
Risk Mitigation Publications
RCN Bulletins
A Newsletter of the DAN Recompression Chamber Network
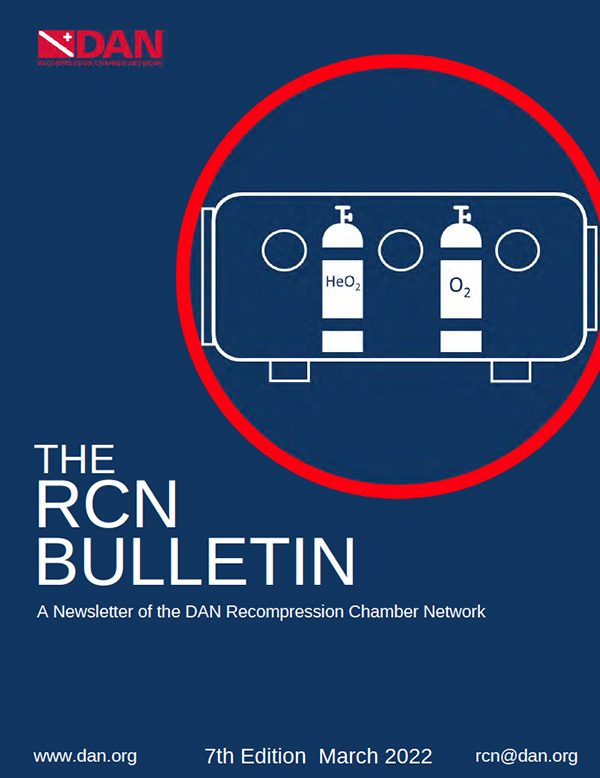
RCN Bulletin Issue 7: March 2022
What’s Inside:
- The Use of Heliox in the treatment of Injured Divers
- Recompression Chambers and Diving Emergencies in Iceland
- Age in the Galapagos
- Remote Chambers: Fernando de Noronha
- Is this Decompression Sickness? Case Studies on Cozumel
- Remote Learning and Education Opportunities for Chamber Operators, Technicians, and Physicians
- Gas Analyzer Calibration for the Treatment of Injured Divers
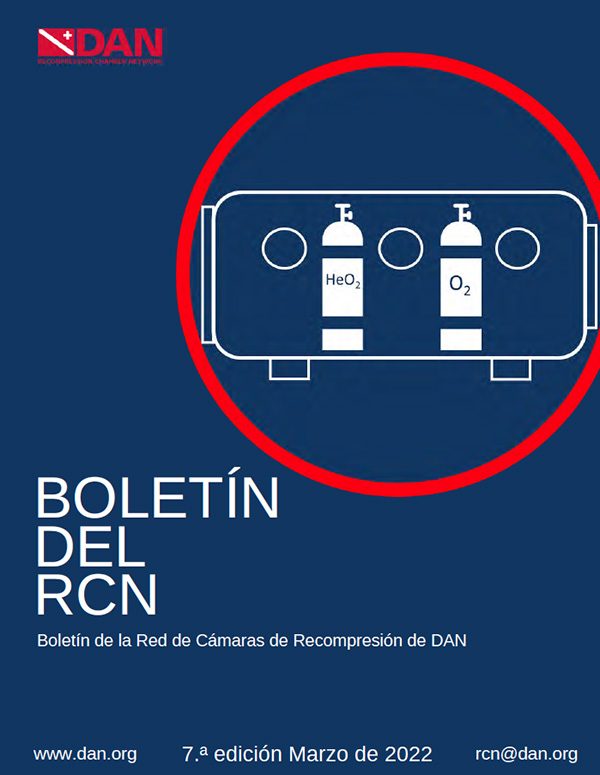
RCN Boletín 7: Marzo 2022 (En Español)
¿Qué Hay Dentro?
- El uso de heliox en el tratamiento de buzos accidentados
- Recompresión y Emergencias de Buceo en Islandia
- Embolismo Arterial Gaseoso en Galápagos
- Cámaras Remotas: Fernando de Noronha
- ¿Es esto una enfermedad por descompresión? Caso de Estudio en Cozumel
- Aprendizaje y educación a distancia: Oportunidades para Operadores de Cámara, Técnicos, y Médicos
- Calibración del Analizador de gases para el Tratamiento de buzos accidentados
Q: Our unit is new and we have so many things to think about. Could you please share with us the 10 most important things that we should focus on from a safety perspective? Our hospital has asked to demonstrate that we are a safe facility.
This is a very valid question and has been asked on several occasions.
While there are perhaps 100 things, if not more, that even the most basic facility will need to consider, we can prioritize these based on a score obtained from a simple risk assessment tool. It is all about the frequency of exposure, the probability that an incident could lead to an accident, and what the likely consequences could be.
Using actual on-site assessments of 150 facilities around the world, here are the 10 primary risks
based on their risk score. You may be surprised by some of these findings.
1) Safety drills not practiced – an emergency action plan may fail if it is not carried out promptly and correctly. We try to avoid accidents from happening, but they do happen.
2) Alternative breathing gas for the operator not provided — remember that in the event of a fire or contaminated chamber environment, it will take time to get the chamber to the surface. The operator must have a safe and non-oxygen enriched gas throughout the process.
3) Emergency operating and medical procedures undocumented – if it is not recorded, then it does not exist! Even if they are perhaps not entirely correct, at least you will be following something.
4) Maintenance system absent, inadequate, or inappropriate — you cannot expect to have no equipment failures, which usually occur at a critical time if you do not take care of your facilities.
5) Leak testing not done — oxygen leaks introduce a fire risk; sensing lines may lead to under-reading of the depth gauge or inaccurate chamber environment oxygen level measurements.
6) Air supply analysis or quality control lacking — you cannot see, smell, feel, or taste most contaminants in breathing gas. It is only through a carefully considered air quality and analysis control system that you can be more assured of safety.
7) Particle filters before regulators are absent — most high-pressure regulator failures are caused by dirt and particulates lodging on the sensing surface of the regulator valve. The downstream pressure will not remain constant and either the breathing device will fail, or the regulator safety valve will pop and likely cause the operator to panic.
8) Standard operating procedures not documented — how can you demonstrate effective and safe practice if everyone relies on what they think is best? If it is not recorded, it does not exist.
9) Oxygen cleaning procedures are not in place — while oxygen cleaning is not required on a regular basis — except in the event of contamination, suspected contamination, or a lack of confidence in how maintenance was done — when it is required, you will need to have at least a basic oxygen cleaning procedure in place. This might be as simple as a procedure for selecting and then monitoring an external cleaning service provider.
10) Operator checklists are inadequate or lacking — many operators become complacent as the awareness of risk diminishes with time and when start-up and shut-down procedures become too familiar. Remember that the risk does not change — it is as dangerous on the first day as it is years later. Documented and recorded checklists, followed consistently and with full attention, will prevent most system-related accidents from happening.
While some of these may come as a surprise, all of these have a significant impact on the safety status of your facility. None of these are difficult to put in place, demonstrate when requested to do so, or present in the event of an incident.

RCN Bulletin Issue 6: August 2021
What’s Inside:
- Challenges of Operating a Chamberon the Panama Canal During COVID-19
- Symptoms After Diving
- Monoplace Chamber Treatment of Decompression Illness: Review and Commentary
- Infection Control in Hyperbaric Chambers: Selecting Suitable Disinfectant Products
- Remote HBOT Safety and Operational Issues: The Need for Experience and Intervention
- Recompression Chambers for Treatment of Decompression Illness
- UHMS Guidelines for Hyperbaric Facility Operations
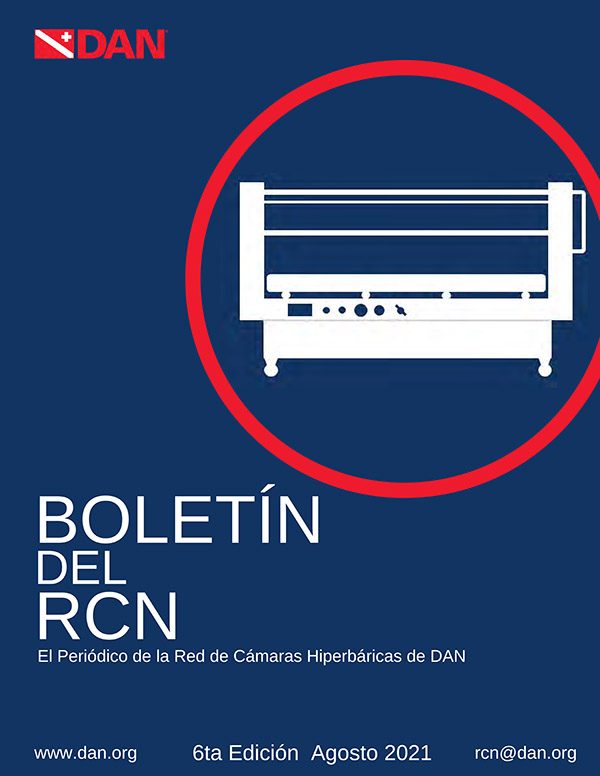
RCN Boletín 6: Agosto 2021 (En Español)
¿Qué Hay Dentro?
- Desafíos de Operaruna Cámara en el Canal de Panamá Durante el COVID-19
- Síntomas Después de Bucear
- Tratamiento de la Enfermedad Disbáricaen Cámaras Monoplaza: Revisión y Comentario
- Control de Infeccionesen Cámaras Hiperbáricas: Selecciónde Productos Desinfectantes Adecuados
- Problemas Operativosy de Seguridad del HBOT Remoto: la Necesidad de Experiencia eIntervención
- Cámaras de Recompresión Para el Tratamiento de Enfermedad por Descompresión
- Directrices UHMS para Operación de Centros Hiperbáricos
Q: We have some rust in our bilge area. Can we fix this ourselves and what should we be concerned about?
A: A chamber would need to have suffered significant neglect before corrosion becomes a major concern; small on-site repairs should be safe and easy to do yourselves.
A decision to perform local paint repairs has two aspects to it: when corrosion damage is too extensive for a local repair by anyone other than a pressure vessel fabricator or repair service, and what should you do when you discover rust.
Steel pressure vessels are usually designed with at least some degree of corrosion allowance, and this is almost always the case where the designer understands the likelihood that moisture can accumulate in hidden places – such as in a bilge. A corrosion allowance is often noted on the nameplate.
In addition to this, the depth of any corrosion is actually less significant than the extent – a small area can withstand a few millimeters of local pitting; an extensive area could well mean that local repair is not possible.
As a guideline, small areas (say less than 12 mm or ½ inch in diameter or length) could allow for material thinning of up to ¼ of the plate thickness or say 1 – 2 mm.
However, several of such pits in a concentrated area (typically 150 mm or 6 inches in diameter or length) where the corrosion exceeds 1 mm could be of concern. In this case, one would need to approach a professional shop or design engineer to evaluate whether local repair would be possible.
A door or viewport flange can sustain more significant damage as long as this is not on the sealing surface.
So, the important thing is to inspect your vulnerable areas regularly and when you notice either ‘crusty’ bubbles, red oxide weeping from a bubble, or simply clear rusting, you should take action as soon as possible. Rust is generally a slow process, but one would want to conduct inspections at least monthly.
Where you notice or suspect corrosion, use a scraper or some other hand instrument to probe the area. Do not use force and certainly do not grind out or use other machine tools to remove corrosion. Once you are able to determine the extent and it appears to be light (less than say 1 mm), use sanding paper or a sanding machine to clean up any rust and the adjacent area at least 25 mm (1”) from any corrosion. Make sure to go down to bare metal. ‘Feather’ the paint where it borders on the bare metal – meaning, lightly sand so that there is no clear ridge between remaining paint and the bare metal.
Clean the area thoroughly, preferably with a solvent or some form of rust converter, and please be very careful when using any flammable liquids in confined spaces – only take a wettened rag into the chamber and not any of the liquid. It is important to remove all forms of oil, dust, debris or fingerprints.
As soon as the area is dry, apply a suitable paint or etch primer. Then allow this to dry and if at all possible, use a fan to circulate the area. Follow the primer instructions as to when it should be suitably dry.
To improve the appearance, you can lightly sand the primed paint to remove any brush marks or raised areas. Be sure to then clean this area as before.
Finally, you can apply the topcoat in one or more layers. Once again, lightly sand the area after each coat has been applied if you wish to make the paint look as pleasing as possible.
Allow to dry thoroughly (usually 72 hours or until ‘dry-to-service’) and be sure that there is no strong or unpleasant odor remaining.
Finally, observe the freshly painted areas after the first few treatments to ensure that there are no bubbles being formed due to any form of oil, dirt or fingerprints that will prevent a firm bonding of the paint to the underlying surfaces.
These minor repairs will be as good as the paint on a new chamber as long as you are sure to remove all the previous corrosion, clean thoroughly between coats, and allow to dry properly between each coat.
The next question will likely be what paint that can be used for these repairs?
You can enquire from a reputable chamber manufacturer or check with the paint supplier, or failing this, any marine application two-part epoxy or two-part polyurethane paint, with a low VOC (volatile organic compound) content and that does not ignite, burn, support combustion or release flammable vapors when subject to fire or heat once applied should be good. You can contact us at " target="_blank" rel="noreferrer noopener">RCN@dan.org if you have any paint-related questions.
RCN Bulletin Issue 5: February 2021
What’s Inside:
- Case Study: Ocular DCS?
- Case Study: Bent in Komodo
- Chamber Air Supply Requirements
- Essential Supplies for a Remote Chamber Setting
- Multiplace Hyperbaric Chambers of Japan
- Unexpected Twists
- Diving Chambers in Indonesia
RCN Boletín 5: Febrero 2021 (En Español)
¿Qué Hay Dentro?
- DCS Ocular?
- Decompresión en Komodo
- Requisitos de Suministro de Aire de la Cámara
- Suministros Esenciales para una Configuración de Cámara Remota
- Las Cámaras Hiperbáricas Multiplaza de Japón
- Giros Inesperados
- Cámaras de Buceo en Indonesia
Q: How often do I need to calibrate my chamber depth gauges?
This question is asked frequently, and some confusion exists with how it needs to be done. There is more to just ‘calibration’ though, so let us break this down into a few respective parts.
- We all use the term ‘calibration’ but in reality, all we can really do to test the gauge accuracy is zero the gauge and then compare the readings with some form of master, or pre-calibrated gauge. Let us therefore accept the word ‘checking’ rather than ‘calibration’, which will indicate if the gauge works and reads correctly.
- Accuracy is a relative term. For deep diving, which decompression must be done very carefully, the standard requirement is ±0.25% of full scale. For a 0 – 450 fsw (0 – 130 msw) gauge, this would imply that each reading needs to be within ±1 fsw (±0.3 msw). However, for the treatment of injured divers to typically no more than 100 fsw (30 msw), this degree of accuracy is not required to ensure the best outcome. Here an accuracy of ±0.5% of full scale is accepted practice.
- The frequency of testing depends on a variety of factors, such as the actual location and situation. Here are the guidelines:
- In the event of any visible discrepancy between different gauges reading the same pressurized compartment (say the Caisson and main lock gauges); or
- In the event of any gauge malfunction, such as not returning to zero, sticking, hunting around the expected pressure level; or
- In the event of any mechanical damage, such as the gauge being dropped or something striking the gauge; or
- Where regulatory requirements dictate (some countries and some operating standards have specified requirements; or
- The original manufacturer’s instructions; or failing any of these
- At least once a year. This is the general international standard; the ASME PVHO-2 standard for example requires annual testing.
- The final consideration is how to check the gauges. Here we have a few options.
- Comparing all the gauges fitted to the chamber: at least the treatment (main) lock and the transfer (entry) lock gauges; the Caisson gauge if fitted; or
- Using a master, calibrated gauge to check each depth gauge at a pre-selected set of pressures going up and down in pressure; or
- Removing the gauge and sending it to an accredited laboratory. However, unless this is required by the inspection authority, this is not the best way to do this as the transporting and then re-installing of the gauge can lead to changes in the readings. The ASME-PVHO-2 standard accepts the first option, as long as it is done thoroughly and recorded.
RCN Bulletin Issue 4: August 2020
What’s Inside:
- Pandemic: An Infection Control Wake Up Call
- In the Treatment of Decompression Illness a Predictable Event on a Remote Caribbean Island?
- Case Study: Split, Croatia
- Challenging CAGE Case Managed Successfully by Recompression Chamber in Remote Location
- Planning for the Future – The DAN Recompression Chamber Assistance Program (RCAP)
- Experiences in Selling, Installing, and Maintaining Recompression Chambers in Remote Areas
- To Drill or Not To Drill… That’s The Question
RCN Boletín 4: Agosto 2020 (En Español)
¿Qué Hay Dentro?
- Pandemia: una Llamada de Atención para el Control de Infecciones
- ¿Es el Tratamiento de la Enfermedad de Descompresión en una Remota isla Caribeña un Evento Predecible?
- Estudio de Caso: Split, Croacia
- Caso Desafiante de CAGE Gestionado con éxito por la Cámara de recompresión en una ubicación remota
- Planificación a Futuro – RCAP, el Programa de Asistencia a Cámaras de Recompresión
- Experiencias en la venta, instalación y mantenimiento de cámaras de recompresión en áreas remotas
- Practicar o no practicar … Esa es la pregunta
Q: Is it safe to use a lithium-ion battery powered device inside the hyperbaric chamber?
Lithium-ion batteries have become the standard for most battery powered devices. In a hyperbaric chamber, we might find them in a diving light for emergencies, an otoscope, or internal analyzer units, but mostly in patient-support medical equipment, including implantable devices glucometer sensor units and pain pumps.
While we all hear the stories of lithium-ion battery fires, the truth is that these are almost all as a result of either recharging issues or mechanical damage. We have not yet heard of an implantable device (such as a pacemaker) burning or exploding.
The biggest risk occurs during recharging and for this reason, one should never recharge any batteries inside the chamber. The best advice is to limit the use of any batteries inside the chamber, but where you need to use them, then consider the following additional recommendations:
- Only use original equipment battery chargers for charging batteries (outside the chamber) and only use the manufacturers specific batteries: care is taken by the device manufacturer to manage recharging loads and to optimize the charge levels in the battery.
- Do not leave batteries on charge overnight, for extended periods or when unattended, and do not keep lithium-ion batteries at full charge levels unless you know you will need them.
- Inspect lithium-ion batteries regularly for any sides of damage, deformation (bulging) or leakage.
- Never tamper with parts of the battery, especially not the casing
- Ensure that the battery leads, contacts and housings are always secure.
- Develop, implement and practice an emergency action plan for any form of lithium-ion battery fire: water will not extinguish a lithium-ion fire; these fires will need foam, carbon dioxide or dry chemical extinguishers to extinguish them, so the best course of action is to lock the device out immediately you detect any abnormal heat, smoke, smell or suspected failure. But most of all…
- Never take high energy devices (those that consume more power) into the chamber, such as cell phones, iPads, laptop computers or personal medical devices that use rechargeable lithium-ion batteries.
Disposable coin-size batteries are not regarded as unsafe, but where possible, these should be checked before each treatment, to ensure there has been no damage and that the batteries are secure. You may wish to read the full article “Use of Lithium-Ion Batteries in Hyperbaric Chambers”, either for free or for a one-hour CHT or nurse CE credit, on the International ATMO site.
RCN Bulletin Issue 3: January 2020
What’s Inside:
- The Essential Attributes of Effective Emergency Action Plans or EAPs
- Inherent Weaknesses in Some Decompression Models
- Case Study: Skin DCS
- The Recompression Chambers of the Red Sea
- Dive Sites and Recompression Chambers of Argentina
- Chamber Profile: Zanzibar’s 2010 Chamber Attendant and Operator Course
- Case Study: Dizziness Following a Dive
- Recompression Chambers in the Pacific Island Region
- Case Study: IEDCS and Residual Dizziness
RCN Boletín 3: Enero 2020 (En Español)
¿Qué Hay Dentro?
- Las Características Esenciales de los Planes de Acción de Emergencia Efectivos
- Debilidad Inherente en Algunos Modelos de Descompresión y Tablas de Buceo
- Caso Práctico: EDC Cutánea
- Las Cámaras de Recompresión del Mar Rojo
- Sitios de Buceo y Cámaras de Recompresión de Argentina
- Perfil de la Cámara: Curso de Operador y Asistente de Cámara 2010 de Zanzíbar
- Caso Práctico: Mareo Tras una Inmersión
- Cámaras de Recompresión en la Región de las Islas del Pacífico
- Caso Práctico: Enfermedad por Descompresión del Oído Interno y Mareo Residual
Q: How often do we need to oxygen clean our hyperbaric system?
To answer this question, we first need to understand what is considered as the oxygen-enrichment level at which oxygen cleaning is require from a safety aspect.
There are many different points of view in this respect. However, the generally accepted ‘consensus’ or ‘ASTM’ limit is 25 percent — not to be confused with the safe operating limit in an air-filled chamber of 23.5 percent.
The important aspect here is that the pressure of gases in the compression and gas delivery systems may well exceed 125 psi (0.86 MPa), which is the limit at which one may use ball valves in oxygen systems. This points to a clear message: we need systems free of any form of fuel in order to prevent catastrophic fires.
All gas systems that convey an oxygen-enriched mixture with more than 25 percent enrichment, per volume, should therefore be regarded as oxygen systems. This means that no hydrocarbons (oil especially), dust, particles or any other potential sources of fuel should be present in the complete system.
So, what then is the cleaning frequency of an oxygen system? Here good practice states that oxygen cleaning should be done on any oxygen-enriched gas system:
- Before the system is put into service for the first time;
- When-ever any contamination occurs or is suspected (such as when disallowed fluids or lubricants or even oil-lubricated compressor air is used);
- When-ever a line (pipe, hose or component) is opened without being handled in an oxygen-clean manner;
- When-ever a replacement part or new item of equipment is installed that is not certified as oxygen-clean;
- When-ever a system is disassembled, serviced or overhauled;
- When-ever any brazing or welding is done on any pipe; or
- When-ever any unauthorized work is done on any part of the system;
If none of these activities occurs, then the system should be left intact and periodic cleaning is not required. In fact, as a piping system can be complex, if all the parts are properly cleaning before initial use, we are more likely to contaminate it than to clean it effectively.
If repairs, servicing, modifications, component replacement and/or system disruptions are required, remember to work cleanly to maintain oxygen-cleanliness integrity at all times.
There is one remaining concern:
What happens when we switch from oxygen to air on our breathing systems, and then back to oxygen from air: oil-lubricated compressor air will not be free of oil unless specifically filtered for this flammable impurity. The air purity limit for oil is ≤ 0.1 mg/m3.
If you are unsure of your air quality, then take a sample immediately after use and preferably before oxygen is put back into the system. This may contaminate your piping system from where the air enters the oxygen lines until the breathing apparatus.
RCN Bulletin Issue 2: August 2019
What’s Inside:
- US Navy Treatment Table 9: Medical and Safety Benefits Frequently Overlooked
- A Chamber Operator’s Guide to Running a U.S. Navy Treatment Table 6
- High-Pressure Gas Storage Cylinders
- Chamber Maintenance Needs
- How Often Do We Need to Change Our Chamber Windows?
- Chamber Profile: Madagascar Nosy Be
- Chamber Profile: Prodivers, Kuredu, Maldives
- Case Study: Urinary Retention and Ataxia
RCN Boletín 2: Agosto 2019 (En Español)
¿Qué Hay Dentro?
- Tabla de Tratamiento 9 de la Marina de EEUU: Beneficios médicos y de seguridad frecuentemente ignorados
- Guía del operador de cámara para aplicar la Tabla de Tratamiento 6 de la Marina de EEUU
- Cilindros de almacenamiento de gas a alta presión
- Necesidades de mantenimiento de la cámara
- ¿Con qué frecuencia tenemos que cambiar las ventanillas de nuestra cámara?
- Perfil de cámara: Madagascar, Nosy Be
- Perfil de cámara: Prodivers, Kuredu, Maldivas
- Caso práctico: Retención urinaria y ataxia
Q: What is the correct pressure for our chamber safety valve to be set at?
There are a few things to consider here.
- Some hyperbaric chambers are designed for depths allowing some degree of commercial diving to be done – say up to 225 psi (± 16 ATA), and many are produced to provide up to a 165 FSW (50 MSW) for a US Navy treatment table 6A.
- The most common treatment table for a scuba diver suffering from DCS is the US Navy TT6, requiring only 29 psi (2.8 ATA). Remember also that oxygen as a therapeutic gas becomes increasingly toxic when one exceeds this pressure.
- Occasionally a facility might also use a mixed-gas treatment table, using heliox or nitrox at 100 FSW (30 MSW).
- The safety of the chamber as a pressure vessel is affected by the maximum air supply pressure that could potentially take the chamber pressure to a level above the design pressure.
- The codes require the safety valve to be set to be fully open at no greater than design pressure.
- Finally, one needs to be able to test the safety valve; preferably while still fitted to the chamber.
Based on the typical requirements for an injured diver recompression chamber, safe practice would thus be a combination of the following:
- Install a safety valve that would be fully open at no more than 10 percent above the maximum, actual treatment pressure. This would prevent taking the patient to below the deepest, safe pressure, or to exceed the safe level for oxygen toxicity.
- Consider an additional safety valve, fitted with an external isolating valve, set to protect against depths exceeding oxygen toxicity levels — typically for the US Navy TT6 table. The isolating valve will allow for deeper treatments to be performed. This is easy to install using a T-piece before the existing safety valve.
- If the compressed air system can exceed the chamber design pressure if either of the two above safety valves have been isolated, then fit an additional safety valve to prevent exceeding the chamber design pressure.
Typical safety valves settings might be:
- US Navy TT6 or equivalent oxygen table, set to 72 FSW (22 MSW or 32 psi)
- Comex 30 or equivalent heliox/nitrox table, set to 108 FSW (33 MSW or 48 psi)
- US Navy TT6A or equivalent deep air table, set to 180 FSW (55 MSW or 80 psi)
Q: Does our chamber need both internal and external hull isolation valves?
Piping which passes through the chamber hull must have isolation (shutoff) valves to prevent uncontrolled pressurization or depressurization of the chamber, or leaks in any of the other gas lines that might affect control of the chamber environment should a malfunction occur. It is preferable to have isolation valves both on the exterior and interior sides of the hull.
This requirement is typically set for commercial and military diving systems. However, many clinical chambers are not fitted with this capability — this is especially true for monoplace chambers.
Recompression chambers used for treating injured scuba divers fall into a unique category — they treat neither fit and healthy commercial or military divers, nor sick patients who may be infirm and difficult to manage.
The key to meeting this requirement is thus the assessment of real risk.
The primary concern is loss of control if a system fails — say rapid, run-away pressurization or depressurization, a safety valve opening well below set-pressure, a bilge valve leaking, or a leak in a pressure gauge line. Without being able to isolate the line, control of the chamber and thus the safety of the occupants would be severely compromised.
Secondarily, there is the concern of an inattentive or even an absent operator on the outside. How would the inside attendant deal with such loss of control?
This means that a lack of control on the outside or the inability to control on the inside, without dual shell valves, would be very difficult to achieve.
ASME PVHO-1, the design code that most chambers are designed to, requires a minimum of an external shell valve on all gas lines into or out of the chamber. A recompression chamber must at least meet this requirement. The unlikely event of an absent, disabled or inattentive operator should be evaluated on a case by case basis, and either a policy put in place for minimum of two people to attend the outside of the chamber, or a fail-safe or dead-man’s switch should be installed that will bring the chamber to the surface safely and shut off all pressurization lines.
Dual shell valves would, however, be good practice for all remote chambers with limited staffing.
RCN Bulletin Issue 1: April 2019
What’s Inside:
- Incident Insight – Underdiagnosed and Underinformed
- Chamber Profile: ResortDoc Seychelles
- Chamber Profile: Hyperbaric Medical Centre, Sharm El Sheikh
- DAN’s Essential Service Providers
RCN Boletín 1: Abril 2019 (En Español)
¿Qué Hay Dentro?
- Analizando el Incidente – Subdiagnóstico y no preparados
- Perfil de la Cámara: ResortDoc en Seychelles
- Perfil de la Cámara: Centro Médico Hiperbárico en Sharm El Sheikh
- Proveedores Esenciales de Servicios DAN
What should we do when an injured diver presents for treatment at our facility, who has in implantable cardiac device in place? Can we treat them?
The primary answer to this question does not lie with the device, but rather with the health of the diver.
The important question to ask is whether the diver was cleared to dive, by their cardiac specialist after the device was installed. If declared fit-to-dive with an implantable cardiac device (ICD) in place, then there is no reason not to treat this diver inside the chamber.
The secondary answers lie in the safety of the device and hence of the chamber.
There are no reports of any ICD having failed inside of any recompression that we are aware of. Most ICD manufactures have issued letter of confirmation that their devices are in fact safe to be used in a pressurized environment; this included devices powered by lithium-type batteries.
The concern that the device will be subjected to elevated oxygen levels is addressed in that being implanted, it is not exposed to the chamber operating environment.
Lastly, in most cases, an ICD is sterilized before leaving the factory using an autoclave. Saturated, hot steam at up to 3 ATA (20 MSW, 60 FSW, 29 psi) and typically 135°C (275°F) for between 4 to 60 minutes is used to destroy any microbes. This environment is much harsher than what is expected inside a recompression chamber.